己二胺中总挥发碱、假硝酸方法优化
王竹青
(万华化学(宁波)有限公司,浙江省 宁波市 315812)
摘要:1,6-己二胺在生产过程中会产生一些总挥发碱(氨、氨基己腈、氮杂庚烷)与假硝酸(可还原性氮)的杂质,总挥发碱与假硝酸会残留到最终的产品中,含量过高会影响下游生产的使用。质检能够更快更准确的出具分析结果,对工艺生产与调整起到重要作用。目前行业内分析总挥发碱与假硝酸用到的方法为《SHT 1498.3-1997尼龙66盐中总挥发碱含量的测定》与《SHT 1498.4-1997尼龙66盐中假硝酸含量的测定》,但是该方法玻璃器具装置比较复杂,组装、清洗、操作上存在人员操作效率低、清洗不彻底、玻璃器具易破碎等,所以不断讨论、探究、尝试,通过玻璃器具装置达到优化方法的目的,优化后的方法,实现了数据准确度高、分析时间短、操作简便、玻璃器具使用少以及安全性高。
关键词: 1,6-己二胺 总挥发碱 假硝酸 玻璃器具装置
1.背景介绍
1.1.工艺反应
1,6-己二胺在生产过程中会产生一些总挥发碱(氨、氨基己腈、氮杂庚烷)与假硝酸(可还原性氮)的杂质,总挥发碱与假硝酸会残留到最终的产品中,控制要求总挥发碱≤10mL/100gHMD,假硝酸≤30mg/kg,如果含量过高会影响下游生产的使用。
1.1.1行标方法
目前行业中用到检测方法都为《SHT 1498.3-1997尼龙66盐中总挥发碱含量的测定》与《SHT 1498.4-1997尼龙66盐中假硝酸含量的测定》,总挥发碱的方法原理为在强碱条件下,将挥发碱用蒸馏的方法,以甲醇为载体,在常压下蒸出,用过量的标准稀硫酸溶液吸收,剩余的硫酸用氢氧化钠标准溶液回滴,计算试样中总挥发碱含量。假硝酸的方法原理为在碱性溶液中定氮合金将试样中的假硝酸还原成氨,用蒸馏法蒸出,用过量的标准稀硫酸溶液吸收,剩余的硫酸用氢氧化钠标准溶液回滴,计算试样中假硝酸含量。
两个分析方法为连续承接性分析,先分析完总挥发碱含量,玻璃器具装置中剩余的样品不动,加入定氮合金后继续分析假硝酸含量。用到的玻璃器具装置如图1。
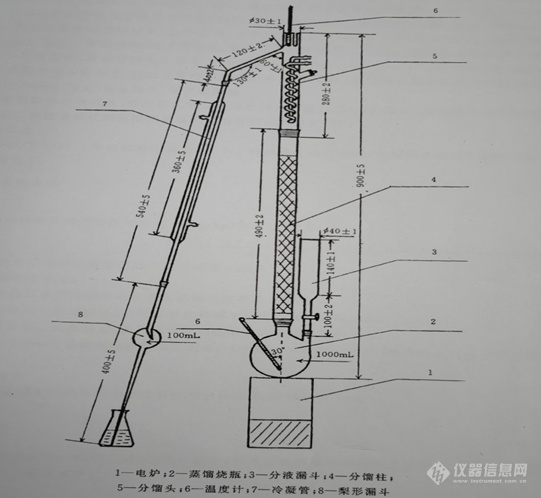
图1
总挥发碱含量分析步骤为:装置(图1)中的1000mL蒸馏烧瓶中放入几粒沸石,加入100.0g±0.1g试样,从分液漏斗加入250mL水、100mL甲醇。在冷凝管出口接上250mL锥形瓶,此锥形瓶中已盛有10.00mL硫酸标准溶液(0.01mol/L)和已加入4滴混合指示液(0.03%甲基红溶液加0.1%亚甲基蓝溶液),使梨形漏斗的出口端浸入溶液中(如图1所示)。加热蒸馏烧瓶至沸腾,从分液漏斗加入100mL氢氧化钠溶液(50%(m/m)),分馏头接通冷却水,回流30min,关闭分馏头冷却水,接通直管冷凝管冷却水,进行蒸馏。终点温度≥96.8℃,蒸馏时间约30min,馏出物体积约为100mL,此时,可关闭直管冷凝管的冷却水,取下锥形瓶,同时接上同样盛有10.00mL硫酸标准溶液和4滴混合指示液的锥形瓶,接通分馏头冷却水,再向烧瓶中缓慢加入(约2min)100mL甲醇,再煮沸10min。然后关闭分馏头冷却水,接通直管冷凝管冷却水,进行蒸馏。控制同样的终点温度和蒸馏时间,待馏出物体积约100mL时,关闭直管冷凝管冷却水,接通分馏头冷却水,停止加热,取下锥形瓶。将两个锥形瓶中的吸收液分别用氢氧化钠标准滴定溶液(0.01mol/L)进行滴定,溶液颜色由紫红色变为绿色即为终点。消耗氢氧化钠标准滴定溶液的毫升数分别为V1和V2。空白试验以水代替试样,按样品总挥发碱含量分析的操作步骤进行空白试验,得到消耗氢氧化钠标准滴定溶液的总毫升数为 V。按照图2的公式进行计算,得到样品中总挥发碱含量。
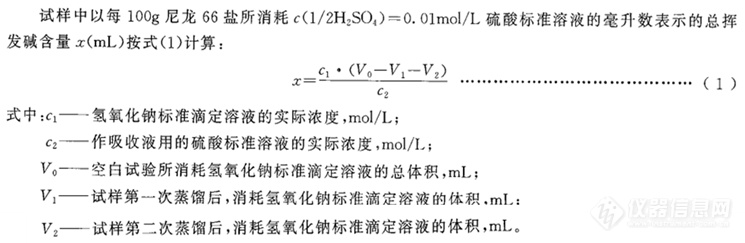
图2
假硝酸含量分析步骤为:按总挥发碱含量方法的规定步骤完成测定后,待图1中蒸馏烧瓶中的液体冷却至30℃~40℃,在冷凝管出口接上250mL锥形瓶,此锥形瓶中已盛有10.00mL硫酸标准溶液(0.01mol/L)和已加入4滴混合指示液(0.03%甲基红溶液加0.1%亚甲基蓝溶液),使梨形漏斗的出口端浸人溶液中(如图1所示)。接通分馏头冷凝管冷却水。从分液漏斗加人30mL甲醇,分批加入2g定氮合金,每次加入的定氮合金都要落在漏斗的底部,打开活塞,用70mL甲醇分数次将定氮合金冲入烧瓶(加完合金约需2min)。缓慢加热至沸,回流30min,关闭分馏头冷却水,接通直管冷凝管冷却水,进行蒸馏,直至终点温度达到(75.0士0.2)℃(约20min),馏出物体积约为100mL为止。停止加热,取下形瓶,同时接上同样盛有10.00mL硫酸标准溶液和4滴混合指示液的另一个锥形瓶,接通分馏头冷却水,经分液漏斗缓慢加入(约2min)100mL甲醇,再加热至沸,回流5min。关闭分馏头冷却水,接通直管冷凝管冷却水,继续蒸馏,直至终点温度达到(75.0士0.2)℃,馏出物体积约100mL为止,停止加热,取下锥形瓶。两个锥形瓶中的吸收液,分别用氢氧化钠标准滴定溶液(0.01mol/L)进行滴定,溶液颜色由紫红色变为绿色即为终点。消耗氢氧化钠标准滴定溶液的毫升数分别为V1和V2。空白试验承接总挥发碱含量空白试验完成后,按样品假硝酸含量分析的步骤作空白试验,得到消耗氢氧化钠标准滴定溶液的总毫升数为 V 。按照图3的公式进行计算,得到样品中总挥发碱含量。
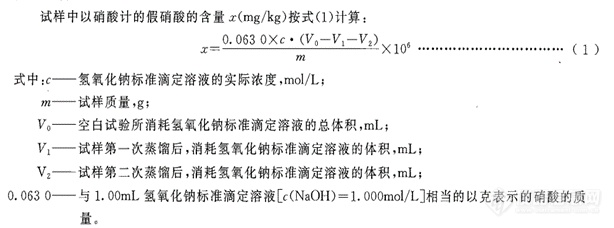
图3
1.1.2.行标使用问题分析
根据以上两个行标要求定制玻璃器具装置,两个方法在操作中存在以下几个问题:1、蒸馏烧瓶中放入几粒沸石,加入试样,必须放入转子,否则会导致蒸馏烧瓶中的溶液受热不均匀,产生憋压喷溅。2、分馏头右侧分流管与主管夹角不能过大,大于60°的话会导致馏出速度严重变慢,甚至很难馏出最后想要的100ml。3、两路冷却水,开关容易混淆。4、分馏柱分馏效果不好会将1,6-己二胺分馏到锥形瓶中导致分析结果偏高。5、人员对比,数据偏差太大。6、分析时间太长,可达12h,期间需要人员一直操作与监督运行。
2.实施过程
2.1.探索与试验
2.1.1.优化分馏柱
在多次试验后跟行业中其他质检进行交流,建议在图1分馏柱内填充玻璃填料,提高分馏效果,防止1,6-己二胺带入锥形瓶中,于是购买玻璃弹簧式填料与空心直行精馏柱,将图1中的分馏柱部分进行替换如图4。
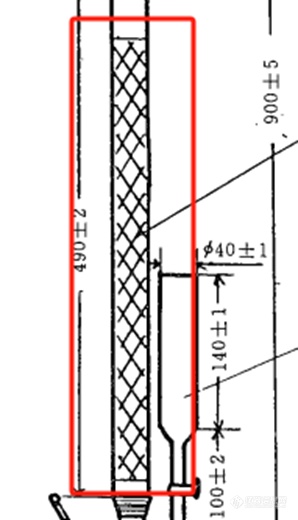
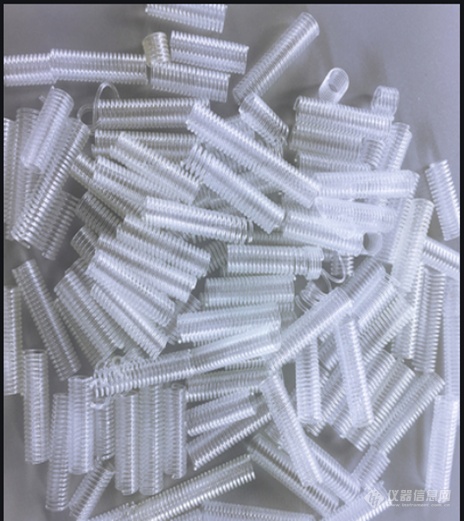
图4
更换后数据偏大的问题有所改善,但是还是不太准确,特别是人员之间或两次试验之间数据偏差较大。另外还有一个问题是定做的分馏头左侧分馏管夹角太大,冷凝回流过去的液体太慢,回流100mL需要1.5h,这样分析一次总挥发碱含量与假硝酸含量需要升温、降温、4次冷凝回流,需要12h,由于人员对比数据偏差较大,期间不能交接,需要同一个人一直做完。如果提高温度设置到油浴150℃,冷凝回流过去的液体加快了,缩短了时间,又有部分1,6-己二胺带入锥形瓶中,导致结果偏大。此可见,该装置需要继续进行优化。
2.1.2.优化整套玻璃器具装置
经过与张聪颖张博士与姜瑞航姜工的交流,讨论分析原理与其他可行性分析方法,经过交流推荐使用图5中的溶剂蒸馏头,该装置本身可进行空气冷凝,于是第一步只使用该蒸馏头进行试验,发现只靠空气冷凝效果不佳,速度太慢;
第二次在溶剂蒸馏头上方增加蛇形冷凝管如图6,冷凝速度非常快,但由于溶剂蒸馏头下方直接接装样品的烧瓶,所以很容易有1,6-己二胺带入冷凝液中。
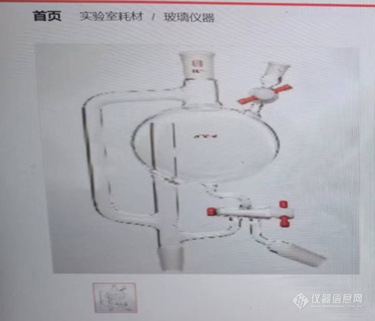
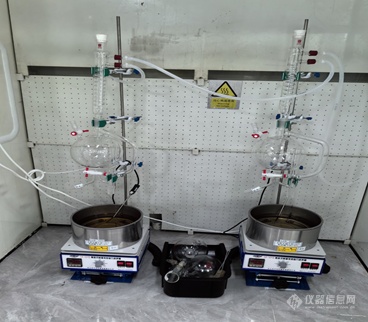
图5 图6
第三次,溶剂蒸馏头下方增加直行冷凝管加玻璃弹簧式填料,并且缩短最上方的蛇形冷凝管的长度,防止整个装置过高,存在安全隐患,如图7。进行试验,分别验证人员对比,并与购买1,6-己二胺检测报告单的数据进行对比。经过对比两种偏差均在允许范围内,见下方“方法验证”中的数据。优化后的图7装置冷凝回流100mL液体的时间大约为20min, 分析一次总挥发碱含量与假硝酸含量需要7h,时间主要消耗在分析完总挥发碱含量后需要将加热油浴冷却至30℃~40℃上,该步骤需要消耗2~3h。
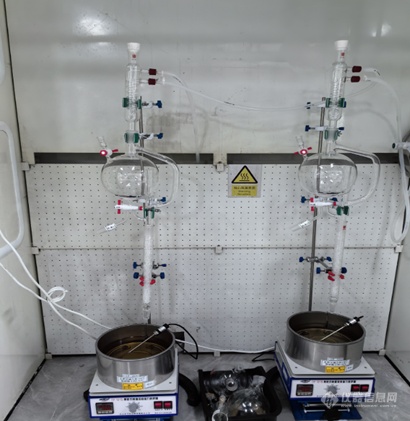
图7
优化后图7的总挥发碱含量分析步骤为:将溶剂蒸馏头的活塞开至“回流”状态,使用甲醇冲洗最上方的冷凝管内壁,精馏柱下方用废液杯接住废液并倒入有机废液中。把 100±0.1g 的己二胺样品称量后放入 1L 的圆底烧瓶里。放入转子。从分液漏斗加入 250 ml 水,100ml 甲醇。打开冷却水,确保溶剂蒸馏头的活塞开至“回流”状态,加热蒸馏烧瓶至沸腾,从分液漏斗缓慢加入100ml氢氧化钠溶液(50%(m/m)),回流 30 分钟。关闭溶剂蒸馏头的活塞,进行蒸馏,终点温度随大气压变化。馏出体积约为 100mL(溶剂蒸馏头大肚上有刻线)。用一次性杯子放置在溶剂蒸馏头外采口处,打开溶剂蒸馏头的活塞开至“外采”状态,馏出液放完后,将溶剂蒸馏头的活塞再开至“回流”状态。向烧瓶中缓慢加入100 mL甲醇(约 2 分钟),煮沸10分钟。关闭溶剂蒸馏头的活塞,进行蒸馏,终点温度随大气压变化。馏出体积约为 100mL(溶剂蒸馏头大肚上有刻线)。用一次性杯子放置在溶剂蒸馏头外采口处,打开溶剂蒸馏头的活塞开至“外采”状态,馏出液放完后,将溶剂蒸馏头的活塞再开至“回流”状态。关闭恒温加热磁力搅拌器“加热”按钮开关。空白试样:以水代替样品,按样品的操作步骤进行空白试验,得到消耗氢氧化钠溶液V0。两次空白、两次样品的馏出液用自动电位滴定仪各加入10mL (1/2H2SO4)硫酸标准溶液0.01mol/L,选择对应的方法进行滴定如图8,电位滴定仪自动计算最终总挥发碱含量。
假硝酸含量分析步骤为:待测定总挥发碱后的液体冷却至 30℃~40℃。从分液漏斗加入 30ml 甲醇,分批加入 2g 定氮合金,每批定氮合金都要落在漏斗的底部,打开活塞,用70ml甲醇分数次将定氮合金冲入烧瓶(加完合金约需 2 分钟)。确保溶剂蒸馏头的活塞开至“回流”状态,加热蒸馏烧瓶至沸腾,回流 30 分钟。关闭溶剂蒸馏头的活塞,进行蒸馏,终点温度随大气压变化。馏出体积约为 100mL(溶剂蒸馏头大肚上有刻线)。用一次性杯子放置在溶剂蒸馏头外采口处,打开溶剂蒸馏头的活塞开至“外采”状态,馏出液放完后,将溶剂蒸馏头的活塞再开至“回流”状态。向烧瓶中缓慢加入100 mL甲醇(约 2 分钟),煮沸10分钟。关闭溶剂蒸馏头的活塞,进行蒸馏,终点温度随大气压变化。馏出体积约为 100mL(溶剂蒸馏头大肚上有刻线)。用一次性杯子放置在溶剂蒸馏头外采口处,打开溶剂蒸馏头的活塞开至“外采”状态,馏出液放完后,将溶剂蒸馏头的活塞再开至“回流”状态。关闭恒温加热磁力搅拌器“加热”按钮开关。空白试样:以水代替样品,按样品的操作步骤进行空白试验,得到消耗氢氧化钠溶液V0。两次空白、两次样品的馏出液用自动电位滴定仪各加入10mL (1/2H2SO4)硫酸标准溶液0.01mol/L,选择对应的方法进行滴定如图8,电位滴定仪自动计算最终假硝酸含量。
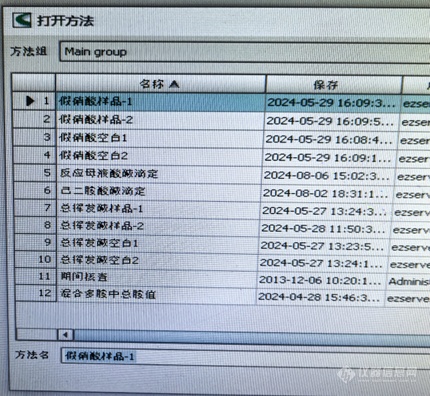
图8
2.1.3.方法验证
对新方法进行准确性验证与人员对比验证。
(1) 为保方法的准确性,随机抽取两批1,6-己二胺的原料进行试验,计算相对标准偏差,判定指标<5%。
组分 | 供应商测定值 | 测定值 | 平均值 | 相对标准偏差,% |
总挥发碱
| 1.23 mL/100gHMD | 1.20 mL/100gHMD | 1.215 mL/100gHMD | 2.47% |
1.14 mL/100gHMD | 1.18 mL/100gHMD | 1.16 mL/100gHMD | 3.45% |
假硝酸
| 24.44mg/kg | 24.85mg/kg | 24.85mg/kg | 1.66% |
19.63mg/kg | 20.17mg/kg | 19.90mg/kg | 2.71% |
总挥发碱含量与假硝酸含量均符合判定要求。
(2) 再现性对比:通过两人进行对比测定,两人结果符合方法的允差,总挥发碱含量≤0.2 mL/100gHMD,假硝酸含量≤3 mg/kg.
组分 | 人员1 | 人员2 | 相对差值 |
总挥发碱 | 1.2753 mL/100gHMD | 1.1965 mL/100gHMD | 0.0788 mL/100gHMD |
假硝酸 | 21.4911 mg/kg | 22.6249 mg/kg | 1.1338 mg/kg |
总挥发碱含量与假硝酸含量均符合方法的允差要求
2.2.收益分析
优化后的方法与原方法相比具有优势明显,主要表现在以下几个方面:
(1) 分析时间大大缩短,操作更加简便
原方法实际操作分为,总挥发碱含量:分析前样品前处理30min-玻璃器具装置冲洗10min-升温15min-回流30min-精馏至锥形瓶90min-添加试剂5min-回流10min-精馏至锥形瓶90min-滴定10min。假硝酸含量:降温150min-添加试剂5min-升温15min-回流30min-精馏至锥形瓶90min-添加试剂5min-回流5min-精馏至锥形瓶90min-滴定10min-清洗器具20min。共需要11h40min。
优化后方法实际操作为,总挥发碱含量:分析前样品前处理30min-玻璃器具装置冲洗10min-升温15min-回流30min-精馏至锥形瓶20min-添加试剂5min-回流10min-精馏至锥形瓶20min-滴定10min。假硝酸含量:降温150min-添加试剂5min-升温15min-回流30min-精馏至锥形瓶20min-添加试剂5min-回流5min-精馏至锥形瓶20min-滴定10min-清洗器具20min。共需要7h10min。
从原方法的11h40min到优化后的7h10min,不仅缩短了分析时间,简便了操作,还避免了班次之间的人员交接。
(2) 提升数据准确度
原方法:玻璃器具装置比较繁琐,精馏液的导出需要较高的温度,会导致分馏效果不佳,精馏液中带入1,6-己二胺导致结果偏高。
优化后方法:玻璃器具装置得到了很大的简化,且为垂直分馏与精馏,空气与水双重冷却,不仅提高了精馏速度,还是的油浴加热不需要太高,避免了原方法中加热温度过高导致结果偏高的问题。
(3) 减少玻璃器具的组成,减少安全隐患
通过图1与图7对比可看出,原方法与优化后玻璃器具装置组成有比较大的差别,原方法玻璃器具需要10个组成部分加2路冷却水,优化后方法玻璃器具需要7个组成部分加1路冷却水。玻璃器具装置从1.5米的左右两侧到1.5米的单侧搭建。在玻璃器具破损、冷却水泄漏等方面的安全性得到了提升。
3.结论
优化后的方法在数据准确度与稳定性上满足使用要求,分析效率、分析安全性上都优于原方法,优化后的方法得到技术工程师的审核通过,可以进行使用。
4.感谢
感谢张聪颖张博士与研发工程师姜瑞航姜工的技术指导;
感谢质检中心技术工程师刘翔刘工的技术指导。